The durability and effectiveness of external insulation are greatly influenced by the quality of its installation.
Choosing an insulation material includes evaluating very different factors:
It is not just a question of the quality of the insulation materials. The preparation of the surfaces, the accuracy of the laying and continuity of the insulation across all surfaces, the care applied in plastering the edges, are all elements that must be taken into account.
Frequently, when insulation is not incorporated into the initial design, or it is being added to an existing building, the complexity of the façades can lead to numerous issues. Features such as protruding elements, columns, pillars, and masonry parapets that are attached to the perimeter walls can complicate and increase the cost of installing insulation.
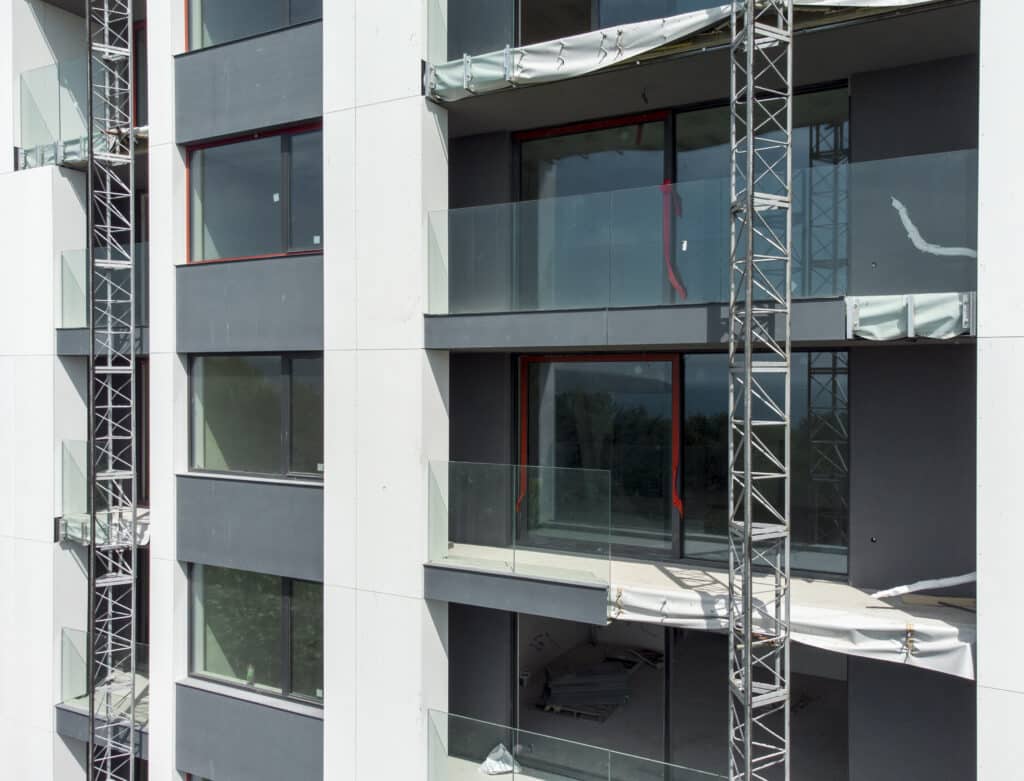
Let's begin by analyzing the meaning of 'ETIC'.
An Exterior Insulation Finishing System (EIFS), also referred to as EWI (Exterior Wall Insulation Systems) or External Thermal Insulation Composite Systems (ETICS), is a cladding system that equips exterior walls with an insulated, finished surface and waterproofing in a composite material system.
Alternatively, an Exterior Insulation Finishing System (EIFS) or External Thermal Insulation Composite System (ETICS) can be described as an energy-saving thermal envelope or cladding insulation that is applied to the external surfaces of a building. It is then completed with a durable, decorative, and protective coating.
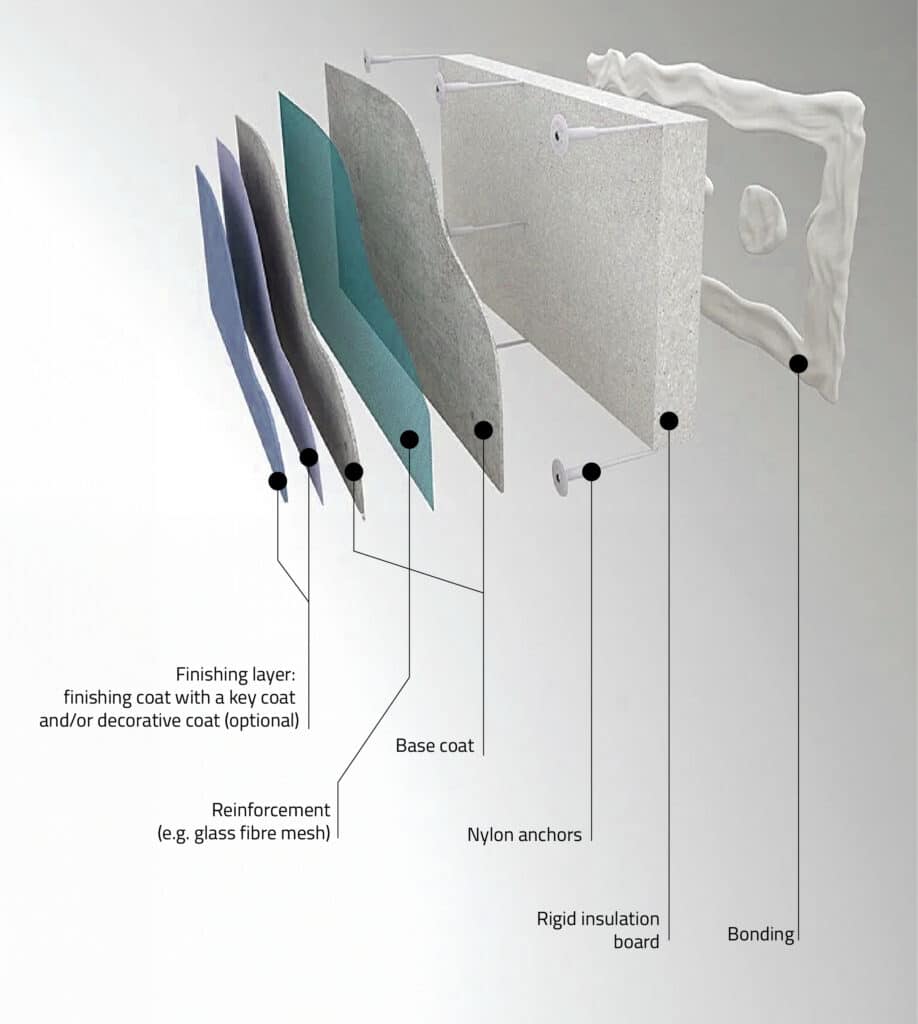
For optimal functionality, EIFS/ETICS must be systematically designed and installed by certified professionals.
The quality and longevity of ETICS are contingent upon the meticulous selection of system components and a correct installation. Manufacturers of ETICS systems, are responsible for ensuring that components are compatible, performance claims are fulfilled, and production performance is consistent. However, the declared performances can only be guaranteed once the insulation is installed following the manufacturer’s installation manuals.
Design plays a fundamental role as the choice of insulation material must be evaluated on the basis of the boundaries defined by the type of structures on which the work is to be carried out, on the compatibility with constituent materials of the original building, on the available budget and potentially also on environmental sustainability in general.
One of the key aspects to evaluate, depending on the level of insulation to be achieved, is how much the application of the coat will influence the design and functionality of the building.
Applying a very thick insulation layer may lead to losing details of the façade's design, there may be problems with the operation of windows and doors, the surfaces of terraces and balconies may be drastically reduced. Some three-dimensional elements may be difficult to wrap.
For this reason, the type of material is very often chosen on the basis of these considerations.
Insulation thickness at the same R-value diagram:
The graph shows the variation in thickness at the same R for different materials available on the market. Very often, the final choice depends on balancing basically 4 fundamental characteristics:
- Compatibility of the insulation with the structures to be insulated (e.g. breathability, workability, thickness)
- Required thickness according to the energy objective to be achieved
- Cost of the material
- Environmental sustainability
Installation of thermal insulation without mistakes: The steps to follow
The installation of a thermal insulation without errors is essential to enjoy long-lasting benefits, it is therefore essential to follow all the phases step-by-step as indicated to correctly lay the external cladding, but, more importantly, it is necessary, before starting the installation of the cladding sheets, to comply with some fundamental rules to avoid problems:
- Carry out a good insulation or energy redevelopment project
- Use quality insulating material (such as) panels for cladding
- Entrust the work to experienced and qualified installers in the installation of thermal insulation
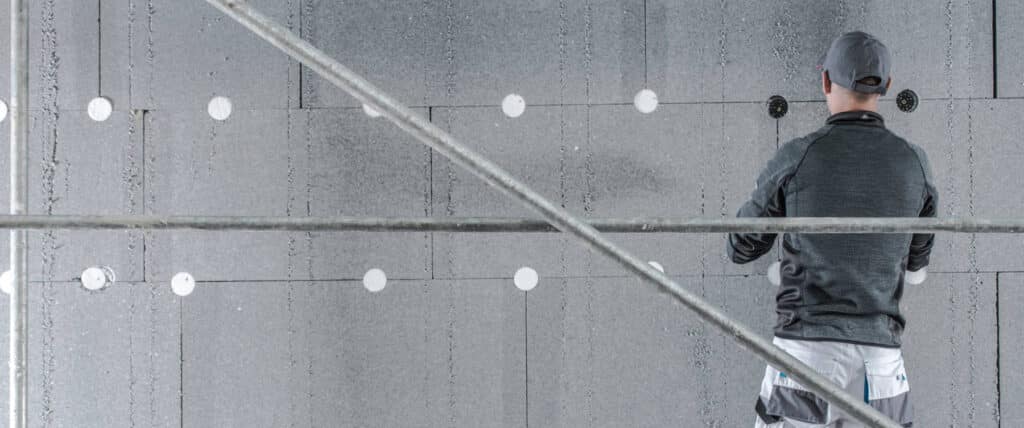
Let's explore the process of applying a thermal coat professionally.
Once a good project has been completed, quality insulating material has been purchased and a skilled installer has been appointed to carry out the intervention, the operational phases for the correct installation begin.
Before starting, it is important to ensure that the material received from the supplier is in perfect condition. The edges and faces must not be warped (e.g. due to tying during transport or impacts). Panels must be delivered wrapped in their original packaging to protect them from the elements. Remember that insulation boards have a very long life when installed. Left exposed to the weather without protection deteriorates their characteristics. The original packaging also has a manufacturer's label with technical details about the product; this is very useful for verifying the characteristics of the delivered product.
Some preliminary information on the worksite organisation:
- It is important to store the materials in suitable places and not exposed to humidity, sun or significant climatic changes
- Create the thermal insulation with temperatures of the masonry and air support between +5 and +35°C in 24 hours
- The masonry support must be preserved from direct sun exposure, if this is not guaranteed naturally, shade by applying adequate shading nets on the scaffolding
Checking the Support and Cleaning
A thermal coat can be installed on different types of walls, from the most common in concrete, but also on walls made of concrete blocks or aerated concrete blocks, on natural stone walls, and even on plastered ones.
Whatever the type of wall that will act as a support for the thermal insulation, it is necessary to verify the adequacy of the wall support through an initial visual check followed by a dusting test, a flatness check and, in the presence of existing coatings such as old paints or plasters, plaster beating and adhesion resistance tests.
After testing, depending on the situation, high pressure washing with disinfectant against micro-vegetation and moss and/or a consolidating agent will be used to prepare the surfaces. Irregularities and gaps in the old plaster will have to be filled, paying particular attention to consolidating the edges of these to avoid detachment due to the stress induced by the drying of the adhesive used to bond the panels.
Installing the Starting Profile:
A very important element for the creation of a state-of-the-art external coat is the starting profile. The installation of a starting profile has two benefits: first of all, it allows the cladding to be lifted from the ground to avoid both direct contact with the floor and infiltration due to humidity or the presence of stagnant water. It is suggested to position the starting profile at a height of not less than 2 cm.
Secondly, it guarantees linearity, in fact the starting profile is useful as a reference for aligning the entire structure of the thermal insulation.
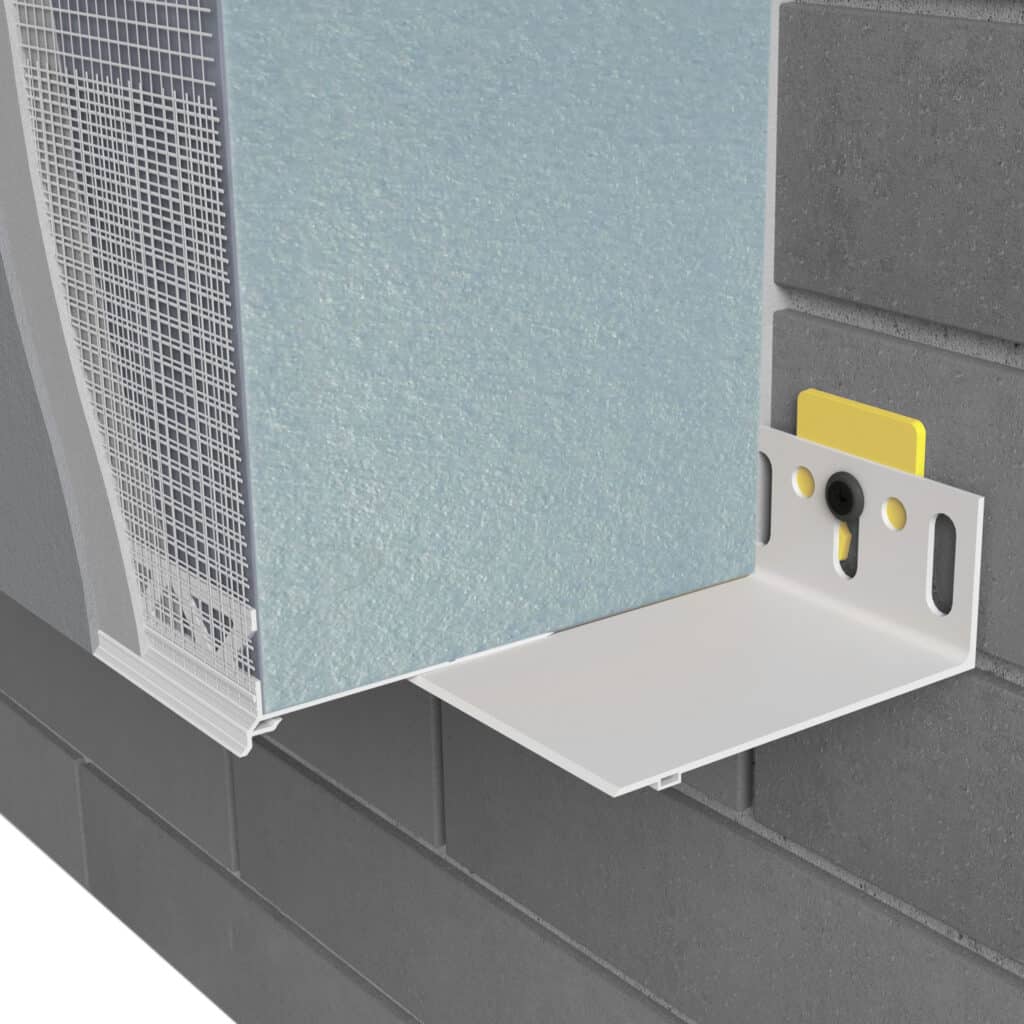
Starting plinth:
To make a long-lasting coat, it is necessary to install at the base, i.e. in the first course of the coat, a starting plinth made of anti-humidity panels, those are normally produced by manufacturers as a specific variant of the basic product.
This attention is even more useful if you do not use a starting profile, in fact, these insulating panels molded in high-density variant of the same material, in addition to being characterized by a high mechanical resistance useful for absorbing blows and shocks, are covered with a "skin" that guarantees low water absorption to preserve the walls from water infiltration and rising damp.
However, it is important to pay attention to a frequent mistake in the production of thermal coats, namely the use of several types of insulating materials with different thermal behaviors.
For this reason, we recommend using products from the same family/manufacturer to cover the entire job.
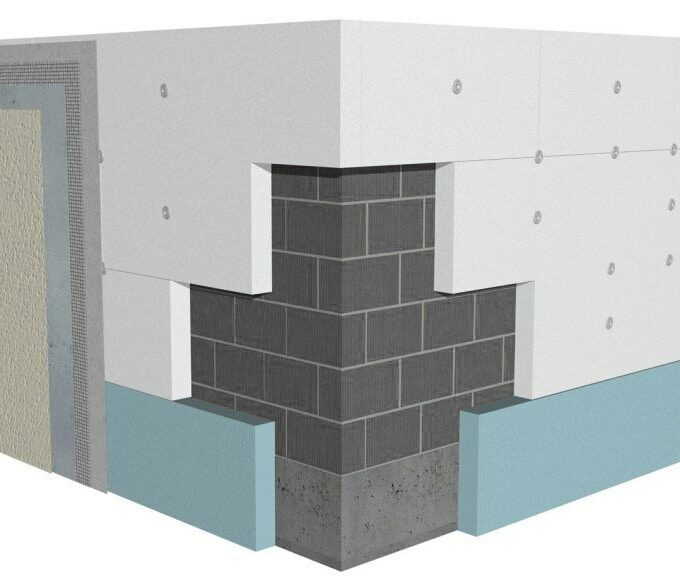
Installation of the cladding panels:
The insulating panels must be laid starting from the bottom to the top of the façade to be insulated and the slabs must be positioned staggered in a brick shape with an offset of at least 25 cm to avoid the formation of joints between the insulating sheets.
Installing insulation panels on a façade in a particularly hot climate such as our, here in Malta can lead to a number of problems related to the rapid drying of the adhesive (choose a suitable product) and expansion/excessive heating of the panels (if they are black or dark grey) while not protected by the plaster/finishing layer. For this reason, companies producing panels of this type often supply a version with a white face. A specific trick to facilitate installation in hot climates.
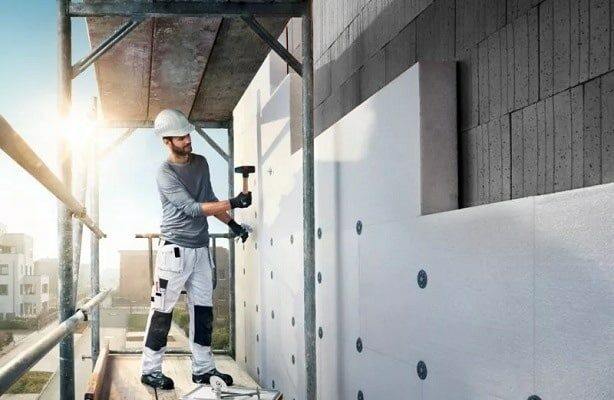
Bonding of cladding sheets:
As already mentioned, for a good insulating coat it is important to choose quality materials, the glue is fundamental but even the best glue on the market whether it is cement-based or foam may not be enough if distributed inadequately. The adhesive must only be placed on the façade to be glued to the wall and not between the panels and must cover at least 40% of the surface of the insulating sheet.
The adhesive can be arranged in beads and points or distributed on the perimeter edge for a width of 5-10 cm and on two or three central points of the slab or on the entire surface and, in this case, the glue can be applied to the insulating sheet with a notched trowel (with variable teeth according to the regularity of the support).
This second gluing system can only be used in the case of really flat surfaces.
Paying attention to gluing is essential to avoid unpleasant problems such as the chimney effect or the mattress effect.
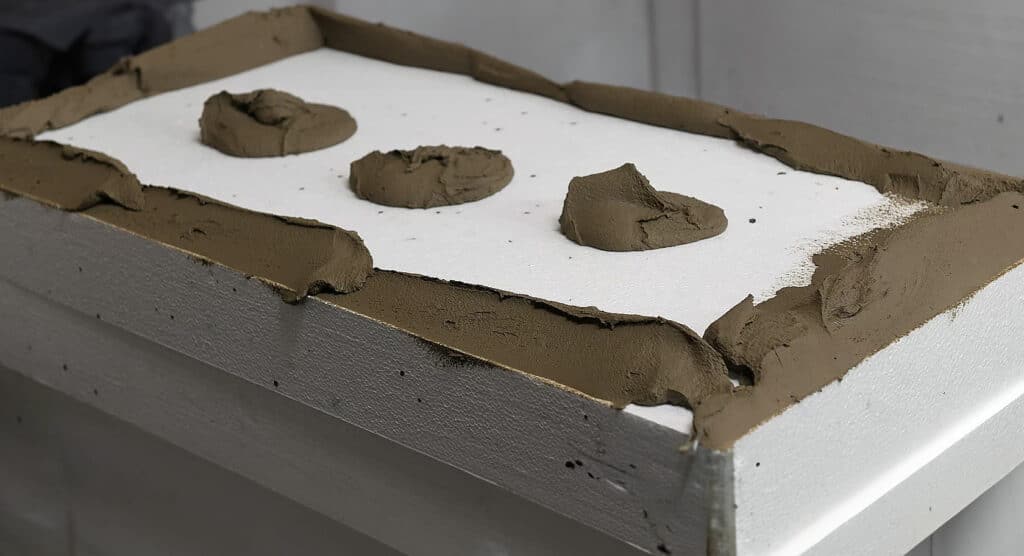
Insulating panels anchoring:
The insulation plugs should be applied 2-3 days after installing the white polystyrene panels, but they should be applied immediately if the insulation is made of EPS with graphite.
The mechanical anchoring plugs must be applied in an adequate number and at established points following the T-shaped or, better, W-shaped pattern and must be chosen according to the wall support so that they do not penetrate too much into the wall, in fact, if the insulation plugs penetrate excessively, there could be a misalignment of the outer layer of the insulating panels with consequent thicknessing in correspondence with the dowels.
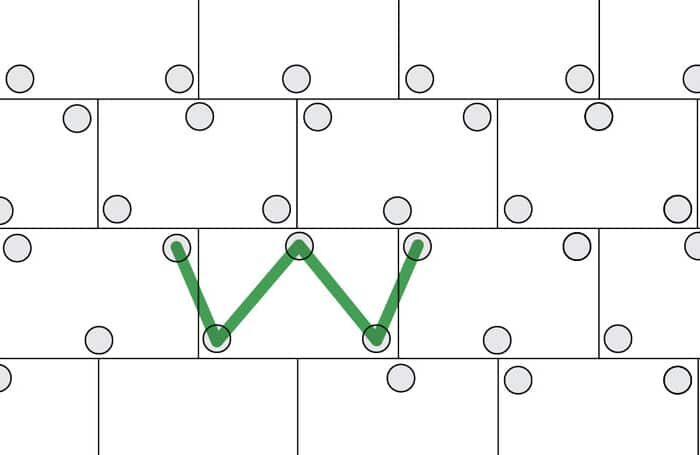
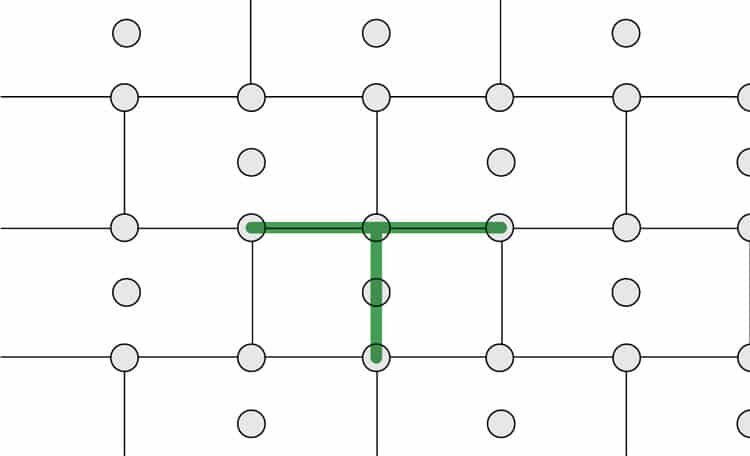
Filling the gaps:
During the installation of insulating panels, cracks may be created between the panels that are not perfectly matched, these joints must be suitably filled with insulating material or, within 5 mm of thickness, with low-density insulating foam. This precaution will be used to prevent the skim coat from penetrating into the cracks, creating differences in thickness and thermal bridges.
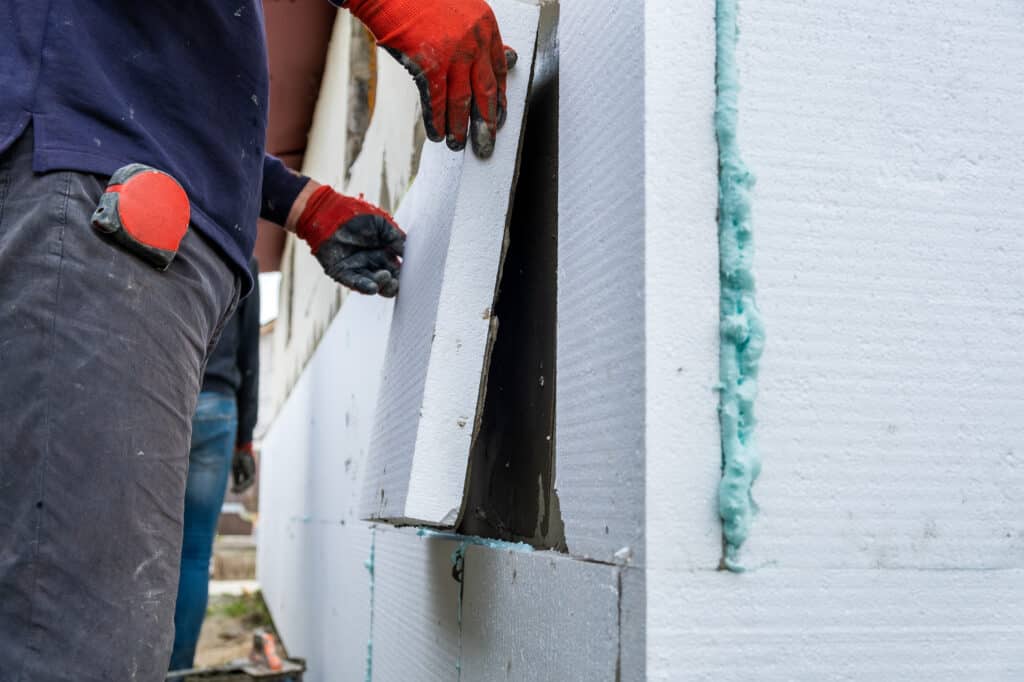
First skimming:
The first skimming of the insulating panels is carried out after 3-10 days, before carrying out this operation it is necessary to eliminate any irregularities of the insulating sheets.
Following the manufacturer's instructions, the base plaster is applied to which the fiberglass mesh is embedded.
Shaving is used with the "fresh-on-fresh" method to ensure the necessary coverage of the entire mesh.
Mesh application for cladding:
The reinforcement mesh is used to withstand the tensions that are generated in the skim coat layer due to temperature changes. It is important to use anti-alkaline coated fiberglass mesh and take care to drown the mesh in two coats of skim coat, to apply the plaster mesh in the center or in the outer third of the base plaster and absolutely not in contact with the insulating panels.
The plaster mesh must be laid from top to bottom and, at the joints, the edges must be overlapped by 10 cm and staggered.
Reinforcements to be made along the aperture profiles:
At the corners of the building and at the edges of door and window apertures, it is necessary to use appropriate corner reinforcements for cladding to preserve the edges from bumps and blows. Moreover, near at the vertices of apertures, it is useful to install portions of cladding mesh arranged at a 45° angle.
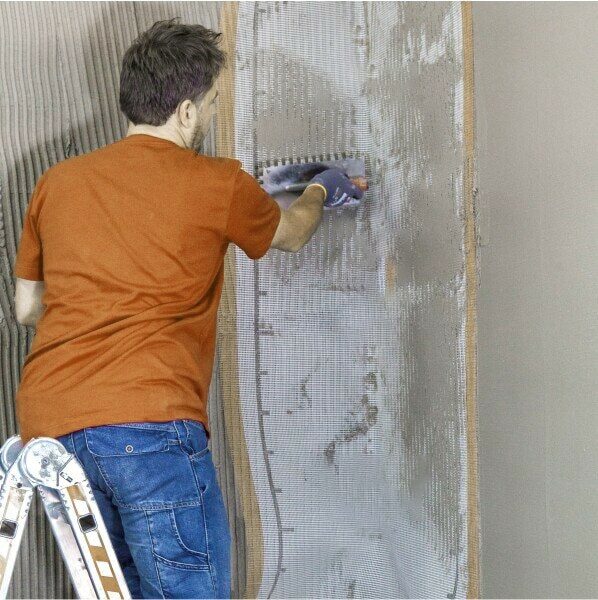
Finishing plaster:
After an adequate period of maturation of the base plaster and after the application of
a primer, it is possible to proceed with the application of the finishing coat.
The façade cladding must be applied in suitable weather conditions that allow it to dry properly, as rain, fog and direct sunlight can have a negative impact.
The thickness of the finishing plaster should be between 1.2 or 1.5 mm.