Insulation materials on the market vary widely and are tailored to meet specific technical needs. Let's examine in detail the most popular products and their ideal applications.
Fibrous insulation is a particular kind of insulation that functions by trapping air within its fibers, thereby hindering heat transfer through convection. Additionally, this insulation reduces heat conduction among gas molecules by decreasing the frequency of particle collisions.
Blanket or roll insulation is among the most common and readily available types of insulation. It consists of flexible fibers, most commonly fiberglass, rock wool and recently also natural fibers which can now be made inert to microorganisms and more resistant to moisture and fire thanks to specific industrial processes. The latter are often used when high environmental sustainability of materials is sought.
Batts and rolls come in widths that match the standard spacing of wall studs, attic trusses, rafters, and floor joists. Continuous rolls can be manually cut and trimmed for a custom fit. They are offered both with and without facings.
Manufacturers frequently apply a facing, like kraft paper aluminium foil, or vinyl, to serve as a vapor and/or air barrier, or to increase heat reflectance. Additionally, facing aids enhance the ease of handling and securing during installation.
These materials are optimal for insulating in scenarios where adaptability to varied spaces is required. Their soft nature allows them to be rolled around structural elements like pillars or columns, wrapped around plant piping, and used to fill intricate spaces and coffers. Their most common application is as insulation for false ceilings and Gypsumboard walls. In such instances, these insulating materials stand out by providing excellent thermal insulation and significantly reducing noise transmission through the walls.
Rockwool or glasswool mattresses.
These panels, also known as mats, were among the earliest forms of insulation to gain popularity in the building market, originally developed for industrial applications with a specific focus on fire-fighting. A key feature of these products is their high fire resistance, rendering them ideal not only for insulation but also for enhancing the fire resistance of structural elements that are inherently vulnerable, such as exposed metal or wooden structures. This, in turn, elevates the overall fire safety profile of a building. Stone wool is noted for its marginally superior fire resistance compared to glass wool insulation.
Insulating performance:
Rockwool or glasswool mattresses generally have good insulating properties, though not as high as rigid panel insulation like EPS, XPS, PUR, PIR, etc. This implies that a greater thickness is needed to achieve the same level of insulation. However, these materials are better suited for application on irregular surfaces, such as creating a counter-wall against a highly irregular stone wall or combining thermal insulation with fire protection, areas where rock or glass wool mattresses excel.
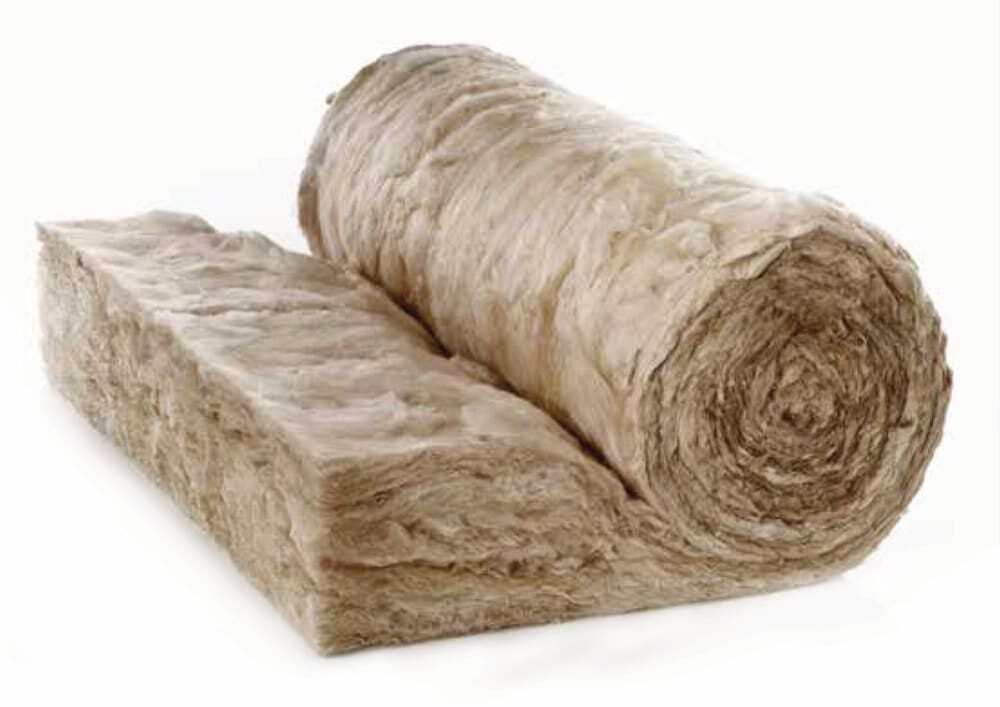
Environmental sustainability:
Rock wool and glass wool originate from natural raw materials: the former is produced by melting basalt rocks and other minerals, while the latter is made from silica sand and recycled glass. Consequently, both materials can be deemed environmentally sustainable. Numerous manufacturers in Europe also propose to reclaim the used material at the end of its lifecycle for recycling, thereby diminishing the carbon footprint of the process even further.
Natural fibers blankets or panels.
An innovative solution in the field of fibrous insulation panels are mattresses made of hemp and kenaf fibres. The strong structure of the natural fibres gives the panel considerable stability and resistance over time, as well as guaranteeing excellent thermal and acoustic insulation performance, superior to other traditional natural-based insulation materials. They are an optimal solution for dry construction and do not release fibres or dust.
Additional eco-friendly solutions gaining traction in the global market include pure cellulose flakes and natural insulating mattresses. These materials have been adapted for use in the industrial building sector through inertisation processes, rendering them appropriate for such applications. Unlike vegetable fiber panels, these alternatives are ideal for filling irregular surfaces due to their soft and pliable consistency. The soft cellulose fibres are blown into compartments under pressure and fit exactly to any shape, so that complete insulation is provided right down to the most hidden corners.
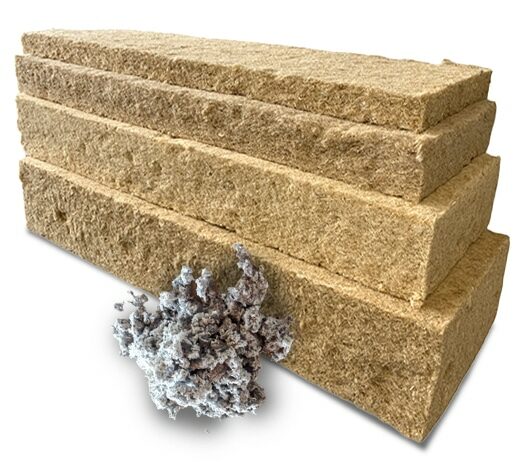
Environmental sustainability:
In natural materials batts, fibres are thermobonded without the use of chemical adhesives, only a minimal amount of polyester fibres can be added, making the panel completely recyclable and environmentally friendly. The exceptional stiffness of the batts resists sagging, ensuring a long service life and maintaining their effectiveness over time without shedding fibres or crumbs. They do not emit VOCs and promote healthy indoor air quality as well as being non-hazardous during installation.
Cellulose flakes are a totally sustainable material being the insulation with the lowest primary energy consumption during production. They are recyclable and in turn originate from recycled material.
These type of insulation can even be carbon-negative, i.e. it captures more carbon than is produced during its manufacture. This makes it an environmentally friendly option for those seeking sustainable insulation materials.
How to correctly install fiber-based mattresses:
During installation, it's crucial to compact the wool in the walls without leaving any gaps, as these can create thermal bridges and significantly reduce the insulation's effectiveness. When filling gypsumboard walls, it's important to fill every space and select the wool density that best meets our needs. Higher density, measured in kilograms per cubic meter, provides better thermal and especially acoustic insulation. However, fitting very dense mats into complex spaces can be challenging, which is why using multiple layers of thinner material is often preferred. Staggering these layers ensures optimal sealing of the joints between the mattresses, enhancing thermal and acoustic insulation. For insulating walls and cavities, the mattresses should be inserted with slight compression to achieve an effective result.
Natural fibers, rock and glass wool and moisture:
There are very different products on the market, some of which have a very high resistance to moisture, a capacity that can be expressed either by the fact that the material is completely impermeable, or that the material is permeable to moisture but the fibres are not damaged by it.
Basically, the issue arises from moisture lurking within the insulation fibers, leading to the growth of microorganisms, bacteria, and mold, which may also compromise the fibers. Even if the insulation remains undamaged, this moisture can cause other complications within the building. To address this, some mattresses include a kraft paper layer that helps regulate humidity. In the case of interior walls or adjacent to insulation walls, a vapor barrier is often installed before sealing the plasterboard panels, sometimes using aluminum for enhanced heat reflection and improved thermal insulation. It is crucial during installation to ensure the kraft paper or vapor barrier joints are properly sealed to prevent moisture from penetrating and becoming trapped inside the insulation.
A vapour barrier, which can be an impermeable or semi-permeable material layer, protects insulation by theoretically preventing condensation within the inner layers. The placement of the vapor barrier is contingent on the direction of heat and vapour flow, typically on the insulation board's warm side. Nevertheless, the application of vapor barriers is widely debated among professionals. In certain conditions, such as during summer, with reversed hygrometric flows, or due to improper installation, the vapor barrier may hinder the building envelope's proper function and compromise the wall's breathability.
Determining the direction of humidity movement is not an easy task, as it depends on the specific indoors and outdoors climatic conditions. In Malta, this is crucial because, despite the lack of dramatic temperature shifts seen in Northern Europe, we experience consistent humidity levels that can quickly fluctuate. Nowadays, the traditional 'Glaser method' has been replaced by predictive calculations in line with EN ISO 13788. This standard is designed to ascertain the minimum internal surface temperature of building components to prevent surface and interstitial condensation. Proper design is key to achieving the desired outcomes.
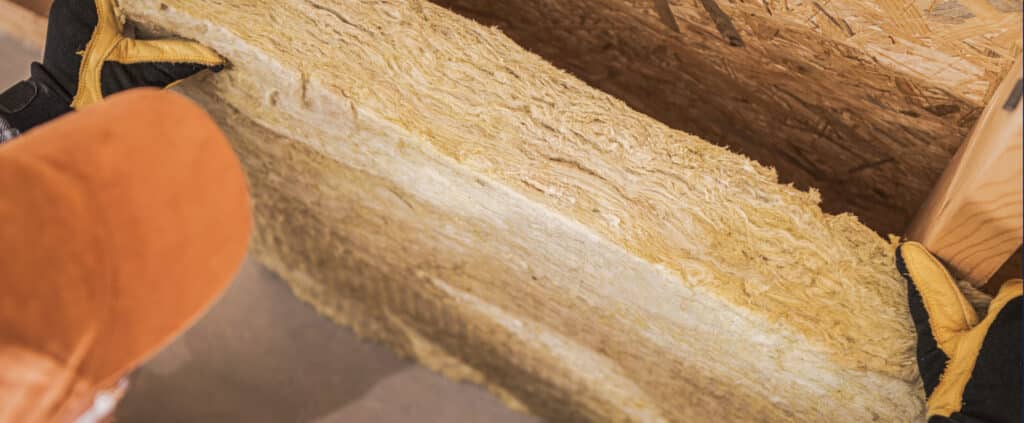